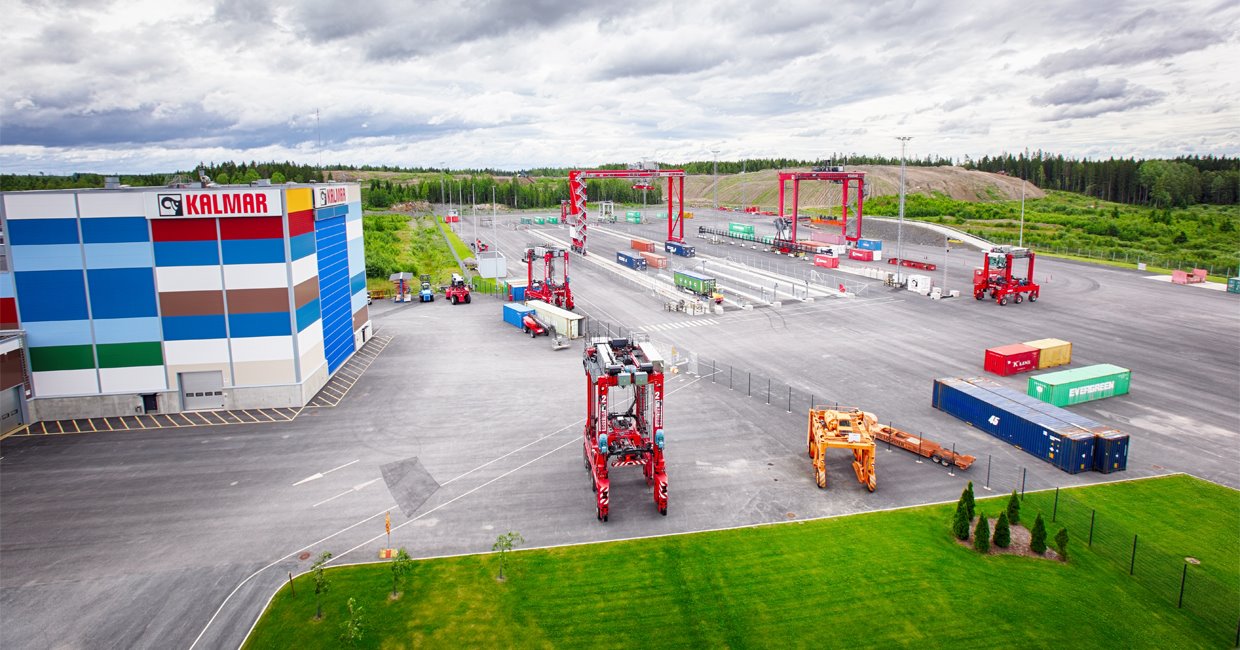
The world’s largest automated inland harbour
One of the secrets to Kalmar's technological leadership in terminal equipment and automation is its Technology and Competence Centre in Tampere, Finland. Here over a hundred R&D professionals develop and test ideas that shape the future of cargo handling.
Kalmar's Technology and Competence Centre is an impressive glass building with straight and undulating lines punctuated by white and red highlights that reflects the very port containers Kalmar is helping to move worldwide. The Centre stands on its own in an industrial area just a fifteen-minute drive from downtown Tampere. It is where world-leading terminal equipment and automation solutions featuring energy efficiency, safety, and intelligent design are born and brought to fruition to join Kalmar's long pedigree of machines revolutionizing port technology.
The secret ingredient is the brainpower, creativity and outside the box thinking of the over 300 people employed at the Centre, nearly one-third of whom are focused in research and development. These best minds in their fields envision, develop, engineer, design, code, prototype, simulate, test and pre-integrate advanced terminal solutions. The work ranges from the small improvements that make a big difference to new product categories all aimed to keep cargo moving fast.
A platform like no other
In 2011-2013, Kalmar invested approximately EUR 35 million in the construction of the centre. In 2015-16, the company has further invested approximately EUR three million in a new port automation testing and development platform.
The new platform is a one of a kind in the world. It is the world's largest automated inland harbour where we can carry out complete end-to-end container handling operations automatically on a small scale, says Tommi Pettersson, Vice President, Software and Automation Development, Automation and Projects Division.
The platform is equipped with the entire set-up: a Navis N4 terminal operating system (TOS), a Kalmar terminal logistic system (TLS) and all necessary automated terminal equipment, such as an automated stacking crane (ASC), automated RTG, automated and manual straddle and shuttle carriers for horizontal transportation, as well as automated truck handling for landside operations & all fully integrated to work together seamlessly.
Major benefits for customers
For Kalmar, the testing and development platform provides it with the capability to test new product features before their market introduction which shortens the time needed to launch new products further upgrades the reliability and quality of existing equipment.
For customers, it offers something unique in the business. First, it enables terminal operators who are interested in automating their container handling operations to see and test a complete automated container yard operation in an unprecedented way. Kalmar is the only supplier in its field to offer this opportunity to its customers.
Second, during the project implementation phase, Kalmar can test and optimise the equipment and software with real and virtual components to ensure their integration with the customer's existing terminal operations before delivery based on real data provided by the customer. This is a great plus. This shortens implementation time significantly at the customer site. As we know, time is money for terminal operators. It is important for them to get things moving fast so that they can do business with their own customers, Pettersson explains.
A third benefit comes from the possibility to train the customer's technicians to maintain the equipment or install software on the testing platform rather than training them after delivery at the customer site. This is a big time-saver.
Once the automated equipment has been shipped, it can be monitored and analysed via a remote connection, even when the port is located on the other side of the world.
Seven R&D laboratories
The Technology and Competence Centre has seven laboratories in addition to the brand new testing and development platform. The more traditional areas & electrical, hydraulics, mechanical and diesel engine laboratories are located in a separate building on the premises.
In addition to these laboratories, the building houses a prototyping workshop. It's where we install new solutions on our terminal equipment before they are ready for the test field, says Pekka Yli-Paunu Director, Research, Automation and Projects Division.
The office building has three other laboratories equipped with the most modern computers, high-end software and virtual environments with modern technologies. As today's focus is on automating terminal operations, a large part of our research and development work is today carried out by sitting in front of computers and coding, says Tommi Pettersson.
The virtual environments laboratory is where software developers are busy working on automatic control systems for the new Kalmar AutoRTG, one of the current spearhead projects. A few desks away, a simulator engineer models the same machine. This laboratory is 'The Place' where new ideas and concepts are integrated and tested together.
A few floors up, we find ourselves in one of the two software development and testing laboratories where test automation engineers and software engineers are busy creating software and testing new innovations using the latest simulated equipment. These days, more and more tests are run automatically rather than manually.
R&D on three fronts
To maintain its leading position in developing automation and container handling solutions in the industry, Kalmar has a multifront approach to R&D at its Technology and Competence Centre. One thing is to try to see what kind of technologies and systems will be available in two to ten years from now and what features we could utilize in our products in the future, says Pettersson.
Of special interest to Kalmar are technologies that include new positioning, perception and human detection systems, and advances in measuring or wireless communication methods.
On another front, R&D activities focus on the company's existing automation solutions and automated equipment to develop them further. And on the third front, we are continuously improving and upgrading our machines. An excellent example of our extensive R&D efforts is Kalmar FastCharge™, the first-ever fully electric powered shuttle and straddle carriers, Pettersson continues.
With this innovative concept, the diesel engine has been removed while the lithium-ion batteries have been scaled up and are used as the only power source. This solution reduces fuel consumption and reduces CO2 and NOx emissions. We plan to do the same with other products and thus boost sustainability in the cargo handling business, Pettersson says.
In addition to sustainability, other megatrends that drive Kalmar's research and development include digitalisation, safety and wireless mobility.
Close co-operation with a business ecosystem
Today, the speed of technological innovations is so breathtaking that no one company can manage it alone. This reality has been acknowledged by Kalmar, too. We use so many different technologies in our operations that we cannot, and do not even want, to develop them all. Instead, we are expanding our business ecosystem. It already includes technology companies, universities and research institutes, Yli-Paunu points out.
Partnership at all stages of the product development process benefits all parties and eventually Kalmar's customers around the world.
The double stackers come with lifting heads with either lift hooks and hydraulic side clamps to handle one or two standard 20-40ft containers, or a lifting head with additional safety wedges that can lock in single containers and handle containers larger than 45ft in length.
“The spreader end beams attachment is a completely new, simplified design that removes the need for hydraulic controlled flow,” says Karlsson. “The installation of the hydraulics has also been simplified with the use of a large main valve that controls lift, lowering and tilt of the mast as well as the attachment.”
Customer feedback indicates that the hydraulic performance in the DCF80-100EC is good enough and the vehicle speed performance can be too high in some applications.
“We have developed two new drive trains, one high performance and one mid performance. The high performance drive train has a similar performance to the DCF80-100, but it is up to 20% more fuel efficient. The mid performance has slightly lower performance, although it is still up to 14% more fuel efficient,” explains Karlsson.
Both drive trains come with three operating modes – power, normal and eco – that can reduce fuel consumption considerably. Easier access for maintenance, longer servicing intervals and advanced diagnostic tools and monitoring systems also contribute to significantly reduced running costs.
Text: Marjaana Lehtinen, Photos: Laura Vesa
Related articles
Further reading
Subscribe and receive updates in your email
Tilaa julkaisujamme